

SDC’s experience has been that all steel mills where we have provided engineering services have crane runways that do not have satisfactory performance.
#Crane girder design to bs5950 pdf code#
The design engineer needs to determine the shear flow in the girder that conforms to zero warping shear stress at the terminal ends of the girder cross section and calculate the torsional warping constant (Cw) in order to apply the code equations. However, for crane girders constructed from built-up sections, meeting the requirements of Section F12 is extremely challenging.
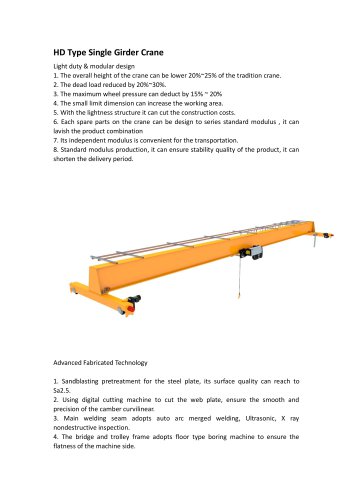
For standard structural sections, meeting the new requirements is not that difficult.
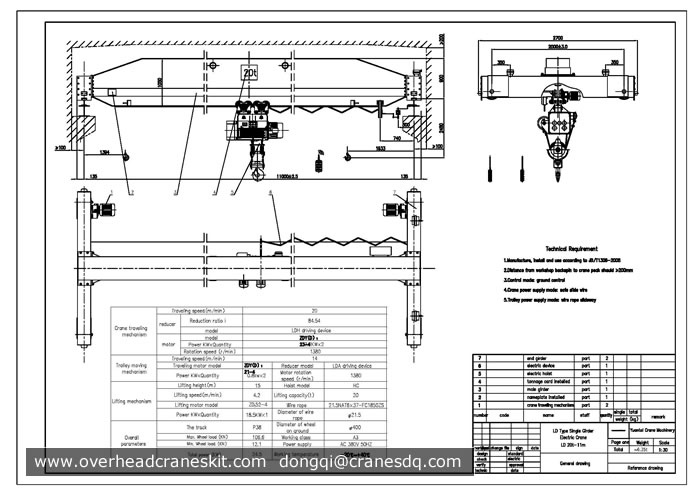
Section F12 has been added to include the design of unsymmetrical structural shapes such as built-up plate girders. The new specification unified the design standards with the most current knowledge and design practices.įor crane runway girder design, the section regarding plate girders found in the 9 th edition of the code has been eliminated. The 2005 AISC Specification integrated both the ASD (Allowable Stress Design) and LRFD (Load Resistance Factor Design) Specifications into a single set of rules for the design of steel structures. AIST states that crane girders designed using the techniques contained in the Technical Report have satisfactory performance without additional strengthening. AIST go on to state that “an exact analysis and design solution is complex and beyond the scope of this document”. AIST states that “the effect of torsional moments and out-of-plane forces at the rail-to-top-flange interface shall be considered”. The August 2003 version of AIST Technical Report 13 has an important change to Section 5.8 for Crane Runway Girders. AIST addresses the design of these unsymmetrical crane girders by determining the effective elements of the girder cross section for X and Y bending stresses. These crane girders are considered to be unsymmetrical. The doubling of the lateral loads for steel mills leads to the design of horizontal thrust plates or horizontal trusses to transfer the loads back to the building columns. The big difference from crane girders used in general industry is both the magnitude of the lifted loads along with the severe crane duty cycles. AISC does not address crane girder design.Īll revisions of AIST Technical Report 13 use flexural analogy. The torsional moment was distributed the top and bottom flanges of the girder by dividing by the girder depth. The torsion load was calculated by taking the lateral load times the depth of the crane rail. The lateral flexural load was resisted by the cap channel, top flange and part of the girder web. Our 1974 crane girder design was based on what is known as flexural analogy. In summary, the steel mill industry requires crane girders to be designed for twice the lateral load as for general industry. The 1991 AIST lateral load requirement has not changed in 30 years as found in the current August 2021 AIST Technical Report 13.ĪISC requirements are now found in ASCE/SEI 7-10 which requires a lateral load of 20% distributed to the crane girders across the bay from each other by lateral stiffness. The load is determined 3 different ways but is generally about 40% of the lifted load distributed to the crane girders across the bay from each other by lateral stiffness. The August 1991 version of AIST Technical Report 13 changed the lateral load requirement to a percentage of either the maximum lifted load or crane wheel load. The August 1979 version of AIST Technical Report 13 specified the lateral crane girder load for a mill crane to be 20% of the lifted load while the AISC requirement remained at 10%. Welds connecting the beam and channel were calculated by determining the horizontal shear between the members.
#Crane girder design to bs5950 pdf manual#
The girder was designed for a lateral load equal to 10% of the lifted load per the 7 th Edition of AISC Manual of Steel Construction. The girder was a standard cross section that included a rolled beam with a cap channel. In 1974 SDC designed a crane girder for an industrial building with a 35T overhead crane. SDC has spent 48+ years designing of crane girders for general industrial buildings and the steel industry.
